CNC machining projects can be exhilarating yet daunting, melding cutting-edge technology with intricate craftsmanship. As businesses and hobbyists alike dive into the world of precision engineering, one pivotal aspect often looms large: budgeting.
The costs associated with CNC machining are as varied as the materials used and the designs conceived. From the initial design phase to the final touches of production, a myriad of financial considerations come into play.
How much will the raw materials set you back? What about machine time and labor? And don’t forget the hidden expenses that can quietly inflate your budget. In this article, we’ll explore vital cost considerations and provide actionable tips to help you master the art of budgeting for your CNC machining projects, ensuring your vision comes to life without breaking the bank.
Whether you’re a seasoned professional or embarking on your first project, this guide will arm you with the knowledge to navigate the complexities of CNC budgeting with confidence.
Understanding the Costs of CNC Machining

Understanding the costs of CNC machining requires delving into a myriad of components that can significantly influence your budget. From the initial setup fees associated with programming and tooling to the material costs that fluctuate based on type and availability, each aspect plays a vital role in your overall expenditure.
Add to this the potential expenses tied to machine operation time, maintenance, and post-processing, and it becomes clear that a simple estimate won’t suffice. Moreover, one must consider how factors such as project complexity, volume requirements, and the precision needed affect pricing as well.
Therefore, it’s essential to approach your budgeting with a comprehensive perspective, ensuring all variables are accounted for to avoid unexpected financial strains mid-project. Engaging with your CNC machining provider early on to discuss these elements can help illuminate the most cost-effective strategies tailored to your specific needs.
When considering cnc services machining, it’s crucial to understand that the costs are not solely tied to the actual machining process. Factors such as the complexity of the design, the type of materials used, and the precision required can all drive up costs.
Additionally, setup times, the need for specialized tooling, and the scale of production runs play significant roles in determining the overall expense. By thoroughly discussing these aspects with your CNC service provider, you can gain a clearer picture of where costs may arise and how to mitigate them effectively.
This proactive approach allows for more accurate budgeting and helps prevent unexpected financial challenges as your project progresses.
Key Cost Factors to Consider

When budgeting for CNC machining projects, several key cost factors must be meticulously examined to arrive at a realistic financial plan. First and foremost, material selection plays a pivotal role; the choice between metals like aluminum or steel can significantly influence overall expenses.
Additionally, the complexity of the design impacts machining time and, consequently, labor costs — more intricate designs demand longer setups and potentially more specialized tooling. Don’t overlook the implications of tolerances and surface finish requirements, as tighter tolerances can escalate costs dramatically.
Furthermore, consider overhead costs, such as machine maintenance, setup fees, and even logistics, which can all add layers of expense to your project. By taking a comprehensive view of these factors, you can create a more robust and adaptable budget that accommodates the unexpected while ensuring quality deliverables.
Best Practices for Cost Management
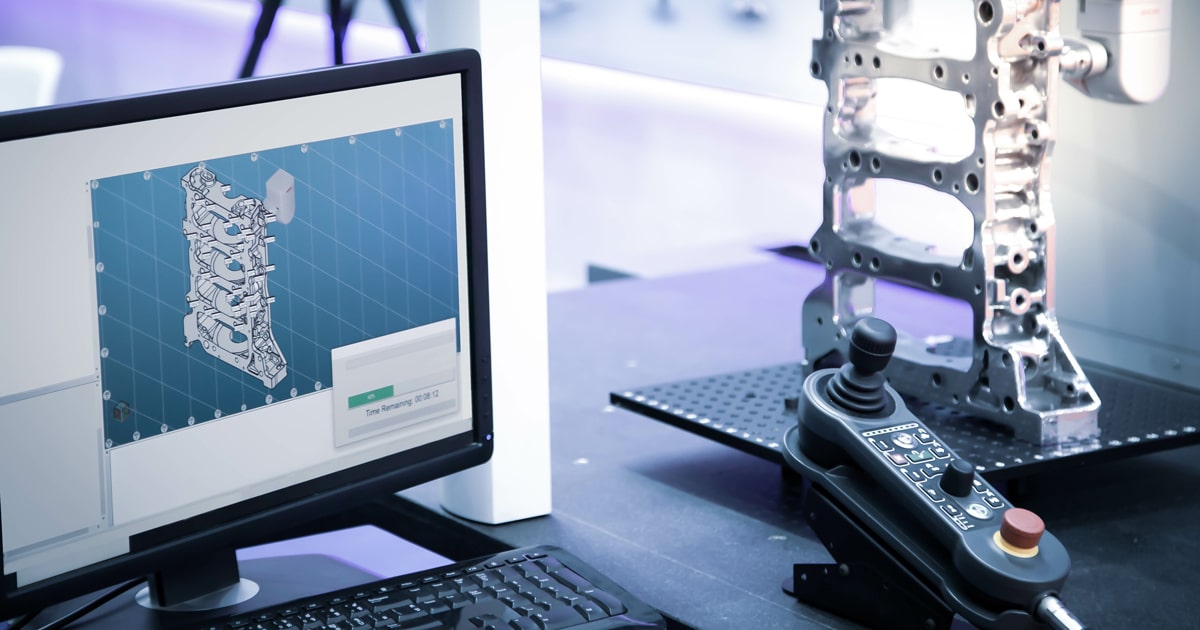
Effective cost management for CNC machining projects requires a strategic approach that encompasses careful planning and continuous monitoring. Start by conducting a thorough analysis of project requirements and potential expenses, from material selection to machining time and labor costs.
Establish a detailed budget that accounts for both fixed and variable costs, ensuring you include a buffer for unexpected expenses that could arise during the machining process. Engage with your suppliers and machinists to negotiate favorable terms that reflect your project’s specific needs; sometimes, building a long-term relationship can lead to better pricing and flexibility.
Regularly review your budget against actual expenditures to identify trends and opportunities for cost savings. Don’t hesitate to adjust your strategies as the project unfolds, and stay open to utilizing alternative materials or techniques that could provide the same quality at a lower cost.
Remember, proactive communication with your team and stakeholders is essential, allowing for transparency and collaboration in managing financial resources effectively throughout the project lifecycle.
Conclusion
In conclusion, effective budgeting for CNC machining projects is essential to ensure that you meet your financial goals while achieving the desired quality and precision in your manufacturing processes. By understanding the key cost considerations—such as raw materials, machine time, labor, and tooling—you can create a comprehensive budget that aligns with your project requirements.
Additionally, exploring different CNC services machining options can help you optimize costs without compromising on quality. With careful planning, diligent analysis, and ongoing communication with your service providers, you can navigate the complexities of budgeting and set your project up for success.